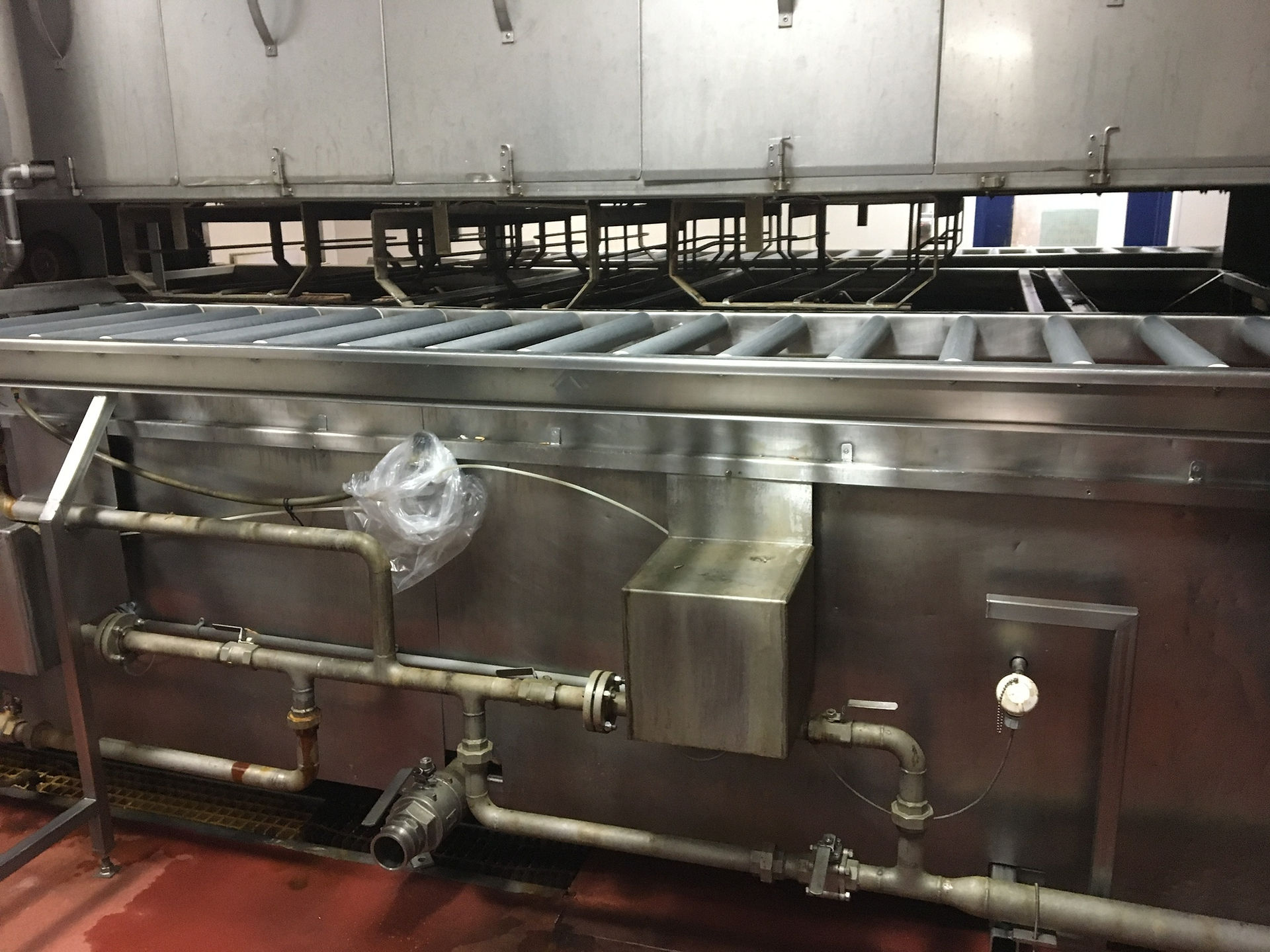
_PNG.png)
Team V-Lobster Raptor:
Austin Murnaghan, Daniel Wartman, & Jesse Currie
​

Design Selection
The team considered various forms of heat exchangers in the design selection process, but determined a static (no flowing fluids) shell-and-tube styled heat exchanger would best satisfy the needs of the client. This was because it could act as an insulated tank so minimal heat was lost overnight and it could exchange the heat from the processed water to the new batch of water at the same time. Next, the team designed a prototype to refine the initially proposed full-scale model.
Prototype
With the help of the fabrication team at the UPEI Faculty of Sustainable Design Engineering, The team designed and built a scaled-down prototype. This served to act as an analog to the full-scale design for verification of its feasibility and simulated heat exchange results. it was constructed with stainless-steel 304 as opposed to 316 to decrease the cost of the prototype as the thermal resistance for 304 and 316 are similar. As soon as it was constructed, the team moved to the testing phase to validate the accuracy of the simulated model.

.jpeg)
Testing
The team conducted two primary tests to validate the accuracy of the heat exchange simulated model. These tests were the Thermal Equilibrium test and the Heat Loss test.
​

Thermal Equilibrium Test
The first test focused on measuring the maximum temperature (equilibrium temperature of the two masses of water) in the prototype and how long it took to do so. It was determined in the prototype this equilibrium temperature was at 70.5 °C and it took just under 10 minutes to do so.

.jpeg)
Heat Loss Test
The second test focused on measuring the final temperature of the supplied water after a period of 12 hours and comparing this result when using various amounts of insulation and reflecting this in the simulated model. It was found this final temperature was around 26-41.5 °C depending on the amount of insulation used. A fluke thermal imaging device was used to monitor the places of significant heat loss during the procedures.


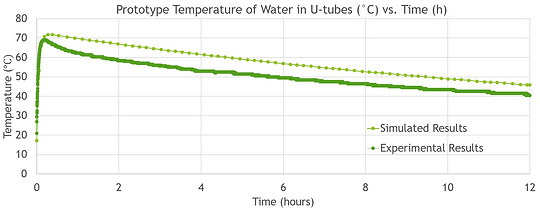
Simulation
The team created a simulation to compare the prototype experimental results to and validate the accuracy of the simulated model so it could be appropriately used for the full-scale model. It modeled two differential equations, one for each energy storing element of the system. These equations were modeled in Simulink and account for conduction and convection heat transfer. The thermal resistances and capacitances were calculated with adherence to the prototype. When comparing the simulated and experimental results, it was deemed to be accurate after refining and accounting for additional heat losses in the simulated model.


Full-Scale Design
Consisting of an insert with 98 individual 166" long tubes welded to the end of a 29.5" auxiliary tank, as well as a cylindrical outer shell 3.9 feet in radius, the full-scale solution is designed to contain 7300 gallons (3650 gallons of processed water and 3650 gallons of newly supplied water). Using the 12 hours between operations, the static shell and tube heat exchanger solution will be able to increase Acadian Supreme's starting water temperature in their water boiler to 49.8°C when used in an enclosure planned to be built around it. This equates to an approximate 40% fuel savings. This would also lead to a $70 000 reduction in fuel costs per year along with other benefits it may provide such as less waiting time for the cooker to heat to 97 °C.